Refrigeration uses a lot of energy and compounds that significantly contribute to global warming, driving the need for alternatives. The 2020 American Innovation and Manufacturing Act, which phases out the manufacturing and sale of products using hydrofluorocarbons, intensifies the need to switch to refrigerants with lower global warming potential.
Against that backdrop, Honeywell Advanced Materials recently announced that its Solstice ze refrigerant, an ultra-low-GWP refrigerant for commercial refrigeration, was found to be 46% more energy efficient than traditional ammonia-based refrigerants when tested on a modular chiller. Solstice 454B, another low-GWP refrigerant in its lineup, can cut 78% of greenhouse gas emissions in residential and light commercial heating and air conditioning compared with traditional refrigerants, the company says. Bosch has said it will incorporate Solstice 454B into its newest line of heat pumps.
Jeff Dormo, president of Honeywell Advanced Materials, has championed hydrofluoroolefins, or HFOs, as an energy-efficient alternative to HFCs. In an interview with Facilities Dive, Dormo explains why swapping HFCs for HFOs will accelerate energy efficiency and weed out the harmful effects of toxic, flammable refrigerants. He also offers other insights on sustainable refrigerants.
Editor’s note: This interview has been edited for length and clarity.
FACILITIES DIVE: What led to Honeywell’s new low-GWP products?
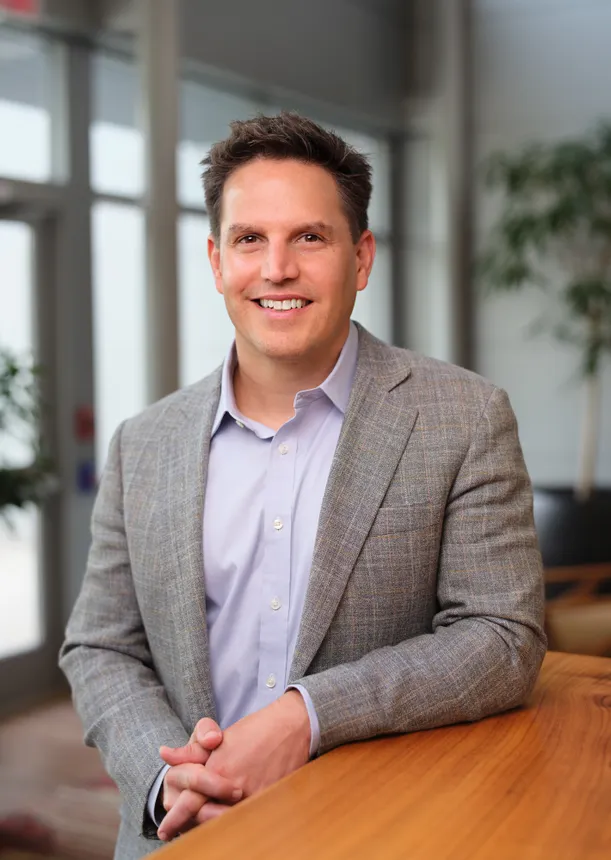
JEFF DORMO: Honeywell continues to focus on investing in cutting-edge technologies that are going to be needed to address the energy transition. We see continuing down the energy efficiency value chain as one of the very important steps for us to do. The Solstice refrigerants used in chillers and the energy efficiency that they bring come from decades of research and development and progressing our knowledge, our expertise in the refrigerant field. That was one of the key problems that we set out in front of us, [how to] drive the innovation toward low-GWP solutions that meet the needs of our customers. And in this case, we think the transition from HFCs to [HFOs] is enabling, as [these alternatives] are going to be cost-effective, safer and energy efficient.
What specific challenges has Honeywell faced in catalyzing the transition to HFOs and how are you addressing them?
The stationary refrigeration market is not as far in the conversion [process] as [automotive and home insulation]. Part of that is because of the variety of applications, like chillers and AC units, which require different solutions. The first big transition that we're seeing will be [the shift from] 410A [refrigerant] to Solstice 454B in 2025. That's about a 78% reduction in GWP.
We're also working on the next-generation of low-GWP solutions for commercial refrigeration applications. In terms of this transition, I’d say we’re in the fourth of fifth inning of a baseball game. It's exciting for us as we tackle these challenges with our customers, focusing on [cost-effectiveness] and how we can get [products] to market quickly.
There have been incidents of ammonia leaks in facilities. Given ammonia’s toxicity, corrosiveness and potential health hazards, what alternatives do you propose?
We see HFOs as a better solution in general. [They are] a nontoxic alternative that is not flammable and continue to be very cost-effective for users. We really want to make sure we're providing our customers with the safest and lowest-cost solutions to meet their needs because we need to create value for [them].
A nontoxic and nonflammable or a nontoxic, very mildly flammable solution is the right answer for many of our customers as they’re looking to transition from some of the toxic gases to something safer if a leak occurs. I think that’s one of the value propositions of HFOs.
You’re looking to launch a new suite of refrigerants in early 2025. Can you tell me a bit more about that?
The next generation of AC refrigerants is coming to market in 2025 [because] the American Innovation and Manufacturing Act requires the phasedown or phase-out and advancement from 410-A [refrigerant]. The next product in that generation [for Honeywell] is Solstice 454B. Beginning Jan. 1, [2025], any new AC units manufactured in the U.S. have to be with a 454B or something less than a 700 GWP level.
To date, as I look at the products that we have [sold] since 2010, it's really eliminated about 395 million tons of CO2 [equivalent] — an admitted equivalent to taking 95 million cars off the road for years [and] 78 million homes running on electricity for a year. Transitioning to 454B is going to continue that trend, and we're excited to see that continue to grow over the years.
How do Honeywell’s foaming agents contribute to boosting the energy efficiency of buildings?
The foaming agents we have are excellent at producing highly insulated foams that increase the energy efficiency of buildings.
In commercial buildings, foaming agents can be additive to the insulation values of foams or other types of insulation. With HFO as that foaming agent, you [can] get an R-value or insulation value that you’ve not been able to achieve through alternative means. As energy efficiency standards become more stringent, HFO foaming agents will be one of those tools we think building owners need in their toolkit.
What are your words of wisdom for commercial building operators and facilities managers looking to implement energy efficiency measures and move to lower global warming potential products?
I think innovation and technology are going to be the key elements of how we address these needs. My business, Advanced Materials, is really focused on materials, innovation and advancement. But, as we look across Honeywell or other places, we're building automation that's really using AI and other technologies and sensors to address the overall energy needs within a building and the safety and quality of the air in the building. If I was talking to the industry, I [would focus on] thinking about how we can use technology and innovation together to solve not just the problems we see today, but also to think forward. To say, “what are the problems in five years? How do we start planning and collaborating together in order to have a solution that's going to meet the needs of the building user?”