Stuart Jailler is director of asset label company Seareach. Views are the author’s own.
A scenario plays out in facilities across industries: operators specify durable asset tags but the purchasing department steps in and questions the cost. A cheaper alternative is chosen and initially everything seems fine. But within a short period barcodes don't scan, labels are missing and facilities teams have to pick up the pieces on a problem they didn't create.
The result? Lost time, increased costs and a tracking system that's not holding together.
Why durability matters
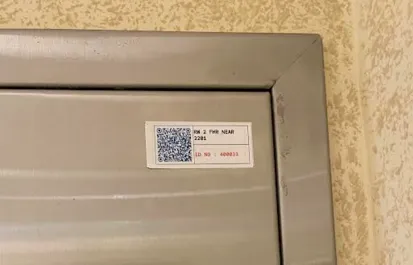
Here's a perfect example of why durability matters.
This fire hose reel inside a hotel is a safety-critical asset, tagged for inspection and maintenance. But let's take a closer look:
It's been printed on an inkjet printer, making it vulnerable to moisture, heat and fading. The adhesive is already failing, meaning it could fall off at any time. If there was a fire — exactly when this reel would be needed — the label would be destroyed within minutes, making maintenance records unreliable.
This is an example of asset tagging done with good intentions but with the wrong materials. The tag itself becomes the weak link in the system.
Expensive mistakes
Low-cost labels might save a few cents upfront but when they fail, the cost of lost asset data and maintenance disruptions can be thousands of dollars. And then there’s the cost of re-tagging.
Common failure points with low-cost labels include —
- Fading print makes barcodes unscannable. UV exposure, cleaning chemicals and wear can cause critical asset numbers to disappear.
- Adhesive failure leads to missing tags. If labels peel off, assets go untracked, throwing off maintenance schedules.
- Material deterioration in harsh environments. Some labels bubble, shrink, or become brittle under extreme temperatures or from chemicals or humidity.
In some cases, compliance is on the line. Healthcare facilities, manufacturing plants and government agencies rely on asset tagging for audits and regulatory checks. When labels fail, the risk isn't just inconvenience; it can mean compliance penalties, asset write-offs and operational slowdowns.
Informed choices
Not all assets need the same type of tag, but a minimum level of durability should be considered.
- Metallized polyester. A step up from standard plastic labels, offering better resistance to wear and moderate environmental exposure.
- Polycarbonate labels with undersurface printing. These can protect printed data from abrasion, chemicals and fading.
- Anodized aluminum asset plates. These labels are gold standard for industrial and outdoor environments, resisting extreme heat, moisture and solvents.
Facilities managers should work closely with purchasing teams to ensure cost-cutting doesn't turn into a hidden liability down the road.
Asset tagging is meant to make life easier, not create problems that have to be solved later. While price is always a factor, the real cost of asset tags should be measured over their full lifecycle.
A label should last as long as the asset it's attached to. When it doesn't, the result is lost efficiency, avoidable costs and unnecessary headaches for facilities teams. Choosing the right tag from the start means fewer replacements, better tracking and a system that actually works when it's needed.